Why 3D-Printed Homes are the Future of Real Estate

Have you ever watched a science fiction movie and thought, "Wow, wouldn't it be cool if we could just print out houses?" Believe it or not, this futuristic idea has now become a reality. In the not-too-distant future, the question won't be whether your next home will be a bungalow or a two-story, but whether it will be traditionally built or 3D printed.
According to a 2022 report by Grand View Research, the global 3D printing construction market was valued at 18.2 million dollars and should continue to grow over the next several years. This trend is set to make homeownership increasingly attainable for many individuals who previously could not afford to purchase a home.
What are 3D Printed Homes
3D printing has only recently started revolutionizing the construction industry, even though it's been present for a few decades. The technique involves using large 3D printers, mounted on robotic arms or gantries, to 'print' houses, layer by layer, much like a baker would pipe frosting onto a cake. This process is called extrusion.
The 'ink' used for printing primarily comprises concrete but can include other materials such as plastic, metal, or recycled waste. Following a digital blueprint or a CAD (Computer Aided Design) model, the printer extrudes the 'ink' in thin layers, layer upon layer, until the structure rises.
This method even allows for creating conduits for electrical and plumbing systems within the home's exterior and interior walls. The size of 3D-printed homes can vary significantly. They can be as small as 500 square feet, similar to a 'tiny home,' or much larger, with some homes reaching beyond 2,000 square feet.
However, keep in mind that 3D printing typically doesn't cover the installation of windows, doors, or roofs, nor does it include interior finishing like painting, flooring, or cabinetry. These are usually added after the basic structure is complete. Nonetheless, some companies are exploring ways to 3D print these components as well.

Advantages of 3D Printed Homes
- Cost-Efficiency: Traditional construction methods can be heavy on the wallet, but 3D printing offers a financially sound alternative. With this technology, companies have significantly reduced labor and material costs, with some claiming to print houses for as low as $4,000.
- Speedy Construction: Gone are the days of waiting months for the construction of your home to finish. A 3D printer can potentially construct a home within 24 to 48 hours, dramatically decreasing the time taken from concept to completion. A Chinese company, WinSun, has reportedly printed a basic single-story, 2,100-square-foot house in just 24 hours (Source: WinSun).
- Unparalleled Customization: 3D printing defies the constraints of standard designs. It enables the creation of houses in diverse shapes and sizes, letting your imagination and creativity guide the blueprint!
- Enhanced Sustainability: 3D-printed homes often promote better eco-practices. They typically use less material and generate less waste than traditional construction methods, making them a greener choice for housing.
Disadvantages of 3D Printed Homes
While 3D-printed homes offer notable advantages, they do come with their own set of challenges:
- Job Displacement: The automation introduced by 3D printing could potentially result in job losses within the construction industry as machines take over tasks traditionally performed by humans.
- Regulatory Hurdles: Not all regions have adapted their building codes to accommodate 3D-printed houses. As a result, regulatory challenges may arise, stunting the implementation of this innovative technology.
- Durability Concerns: Although 3D printing technology continues to advance, doubts about the long-term durability of 3D-printed homes persist, especially when compared to houses built using traditional construction methods.
Costs Associated with 3D-Printed Homes
The tantalizing promise of affordability stands as a major draw for 3D-printed homes. While costs vary greatly depending on location, design, size, and specific technology utilized, these homes are often significantly more cost-effective than traditional properties.
The potential for savings stems largely from reduced labor costs, as 3D printing is mainly automated. Additionally, this construction process tends to use less material since the printer only applies what the design requires.
For instance, ICON, a Texas-based company, reportedly constructed a 350-square-foot house for around $10,000, encompassing both materials and labor. This price is merely a fraction of the cost of a similarly sized traditional home.
Wolf Ranch Genesis 3D-Printed Homes
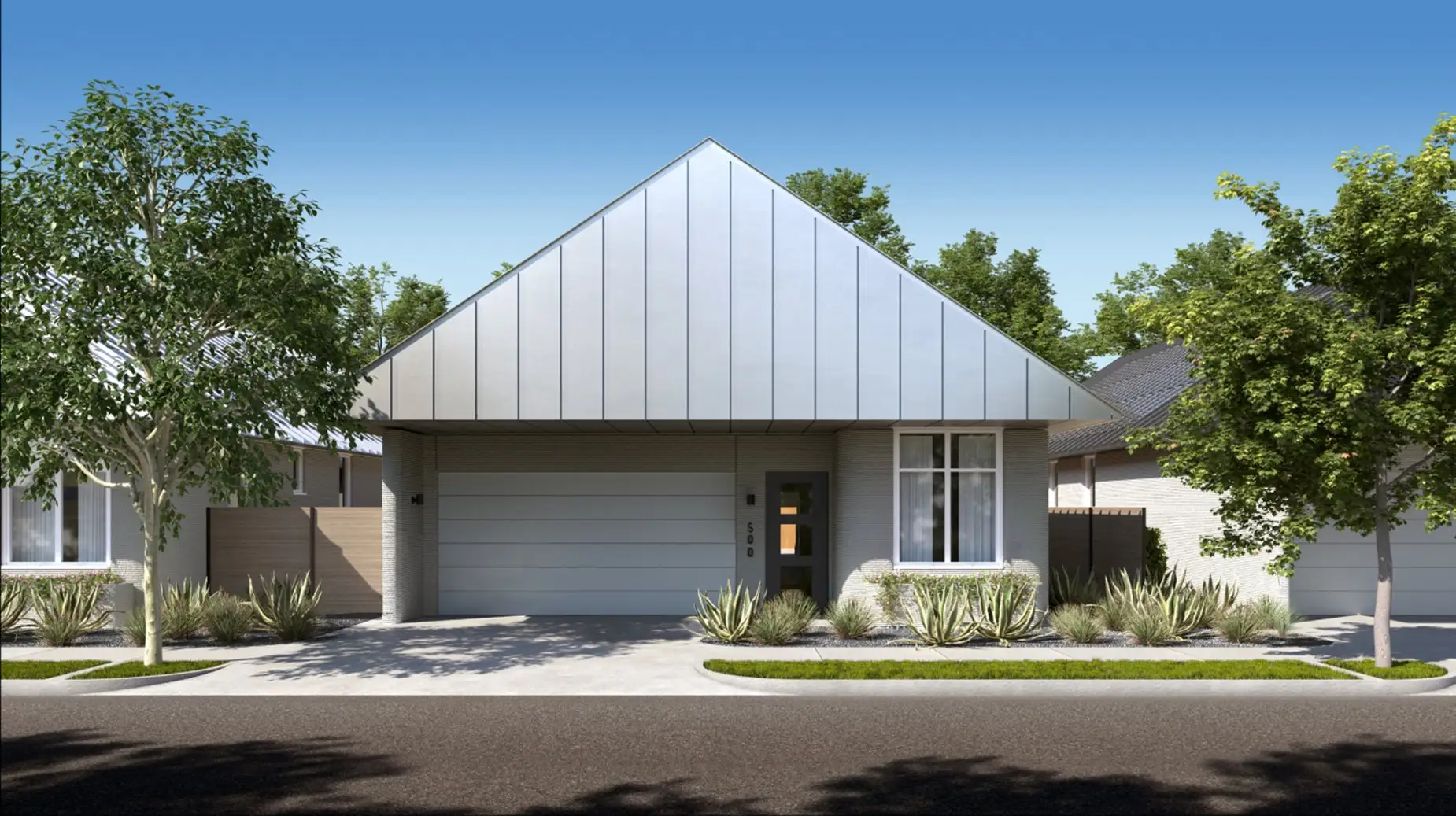
One example of a new 3D-printed community is Wolf Ranch Genesis, located 25 miles north of Austin in Georgetown, TX. This unique neighborhood will feature 100 homes, with each property presenting one of eight distinctive floorplans.
In a nod to sustainability, each home will be powered by the sun, utilizing rooftop solar panels. Additionally, all houses will have connected home features and the Wolf Ranch security package, ensuring a modern and secure living experience. Residents will also have access to on-site state-of-the-art amenities like a playground and pool in this conveniently located community.
The Future of 3D-Printed Homes
While still relatively young, the field of 3D-printed homes is experiencing rapid growth. As this pioneering technology evolves and matures, it's gradually penetrating the mainstream real estate and construction industry. Consequently, the once-revolutionary idea of 3D-printed homes is starting to become a common sight in our neighborhoods.